滁州发那科数控系统维修案例分享
物理磨损/加热 每台机器都有****佳的运行寿命。随着机器的老化,工业机器的磨损会导致令人望而却步的结果。这种磨损会导致轴承失效、金属疲劳、腐蚀、不对中和表面退化等问题。 解决方案:跟踪这种恶化很重要。人工智能主导的预测性维护可以通过持续跟踪机器参数并及时通知工厂工程师,在机器发展到严重水平之前帮助指出机器的退化。 流程效率低下 流程效率低下的定义是为了完成相同数量的工作,需要过多的投入(电、热或其他原材料)。流程效率低下会导致运营成本过高,并且通常表明存在可能增加事故/机器故障机会的问题。 解决方案:优化设备性能是一个困难的话题,因为变化非常小,甚至计算损失也很棘手。按照惯例,制造商会要求主题**检查设置和流程,分析运营数据并提出流程改进建议。但是随着中小企业的退休和传感器数据的****,坚持这种模式是不合理的。像 UptimeAI 这样的虚拟 AI **解决方案可以帮助跟踪性能曲线的效率,并指出资产运营中的小低效可能是救命稻草,尤其是在当前远程优先操作的趋势下。西门子数控系统808D系统维修-显示报警代码69000.滁州发那科数控系统维修案例分享
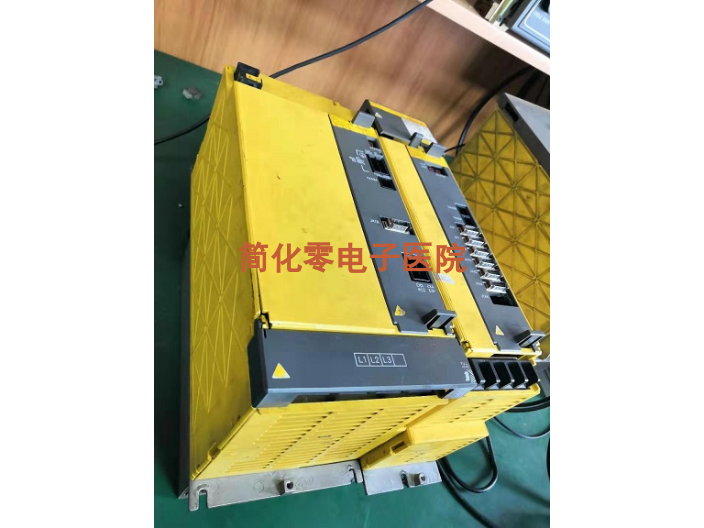
测试电机短路的正确方法是什么?对FANUC 电机 进行短路故障排除的正确方法是首先锁定机器,从驱动器上拆下电缆,并用兆欧表测试所有三个电机相接地。这将测试电机和电缆是否存在问题。 当连接到 FANUC 驱动器的 RS-232 端口时,为什么会出现错误? 这些错误有多种解释。RS-323 端口是FANUC 驱动器上的高故障组件,因为它非常容易受到电涌的影响。但是,RS-232 电缆也是另一个高故障项目。确保您使用的电缆在通信时可以正常工作。否则,当您尝试读入或拔出电缆时,您将收到 086 警报,指示电缆不正确或端口出现故障。滁州发那科数控系统维修案例分享哈斯CNC数控系统故障分析及维修.
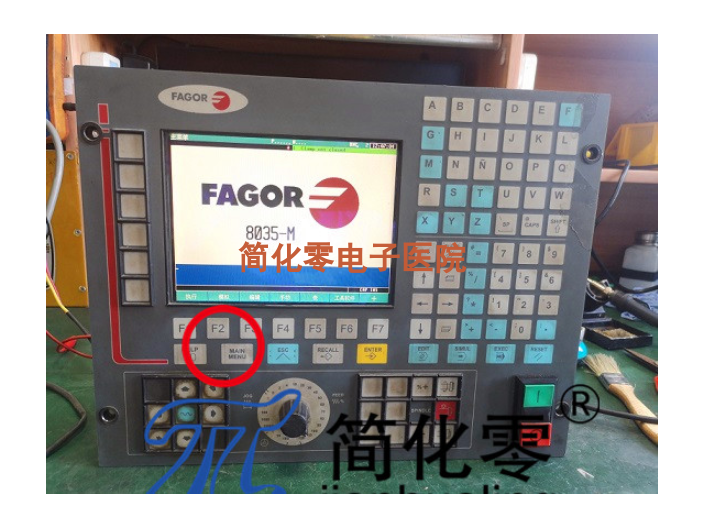
重新写入伺服系统软件并进行伺服初始化,如果系统恢复正常运行,则故障是由系统伺服软件不良造成的 3.检查伺服模块连接的光缆或电缆是否接触不良或折断,如有问题更换光缆或电缆 4.更换轴控制卡,并进行伺服初始化操作,如果恢复正常,则故障为轴控制卡故障 5.更换系统CPU,如果系统恢复正常,则故障为系统硬件或者****电路造成的 6.如果按以上步骤操作后,还是920报警,那么更换系统主板 让我们看看所有不同的警报、触发它们的原因以及如何在这些 易于遵循的步骤中****它们。
要测试电缆或端口是否出现故障,请取一根已知良好的电缆并将其插入 RS-232 端口。接下来,设置您的机器以接收文件。屏幕应闪烁“READ”。接下来,将您的文件传输到机床中。如果机器继续闪烁“READ”(或现代控件上的“LSK”)但从未接收到文件,则内存板或主板上的通信端口有缺陷。这些板或您的机器将需要送去维修。 什么是轴通信错误? 轴通信错误表示电机编码器和 CNC 控制器之间的通信问题。这可能是由电机编码器本身、连接到编码器的电缆或电缆插入的轴控制卡引起的。西门子810D数控系统维修报警70001故障.
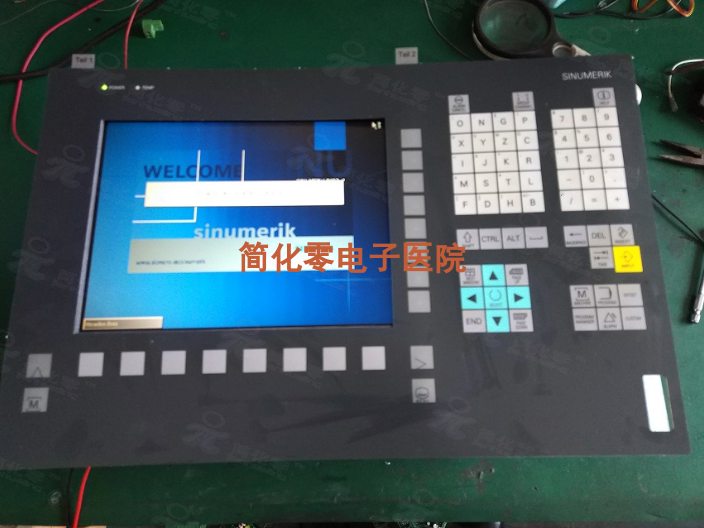
德玛吉机床维修保养 正确维护德玛吉德玛吉机床和机器零件是从性能和耐用性角度避免问题的****方法。无论是附件、清洁还是例行检查,保持机械工具处于****新状态是必不可少的。如果维护没有被优先考虑,那么从业务和生产的角度来看,很可能会发生巨大的损失,而没有人愿意遇到这种情况。 1、德玛吉机床润滑: 对于任何自动化机器,润滑是****重要的事情之一。通常,定期检查润滑水平是一个很好的起点。如果您在一段时间内发现润滑水平下降,请务必安排每周检查并仔细监控。定期保护机器的电机,包括对其运动部件进行上油和润滑是不可避免的。德玛吉机床海德汉cnc系统主机51故障代码维修.滁州发那科数控系统维修案例分享
法那科主轴驱动器显示03代码怎么解决.滁州发那科数控系统维修案例分享
际使用中确保了我们 CNC 软件的人机工效。此外,西门子还是增进产品持续性与能效方面的先行者,西门子机床控制系统在机床节能设备领域始终保持着lingxian地位。适用各种行业的理想解决方案在持续的人口增长和不断增加的通信资源需求等全球性趋势下,汽车、航空航天、发电、医疗等众多领域面临着新的挑战。西门子机床控制系统与这些机床市场紧密,从而生 产出适应市场需求的 SINUMERIK 产品。出色的 IT 集成产品和服务我们还提供了先进的 IT 集成产品和模拟解决方案,非常适合于网络化生产和 IT 环境;其中涵盖了行业****的支持与服务系列方案,确保了的生产、服务和维护。因此,SINUMERIK 行业解决方案能够在全球遍地开花。 滁州发那科数控系统维修案例分享
上一篇: 滁州发那科伺服电机维修价格
下一篇: 滁州人机界面触摸屏维修厂家